Density, level measurement and point level detection in coke drums
Category: Refining and petrochemical
Specifications
Details
Coke drums
Density, level measurement and point level detection in coke drums
Process data
Measuring task
Density and level measurement, point level detection
Measuring point
Tank
Measuring range up to
18 m
Medium
Heavy residual oil
Process temperature
+400 … +480 °C
Process pressure
+3 …+8 bar
Special challenges
High temperature, heavy foam, buildup
Application
Delayed coking units are a critical step in the refining process - this is where downtime, inefficiency, and overfill are not an option. They generate extreme heat during operation and are very large vessels. By monitoring upper vapour phase density, operators can reduce antifoam carry-over and improve continuous productivity with accurate level measurement.
Your benefit
Reliable
Safe measurement even under extreme conditions
Cost effective
Reduced need of foam agents thanks to continuous foam monitoring
User friendly
Easy installation
Recommended products
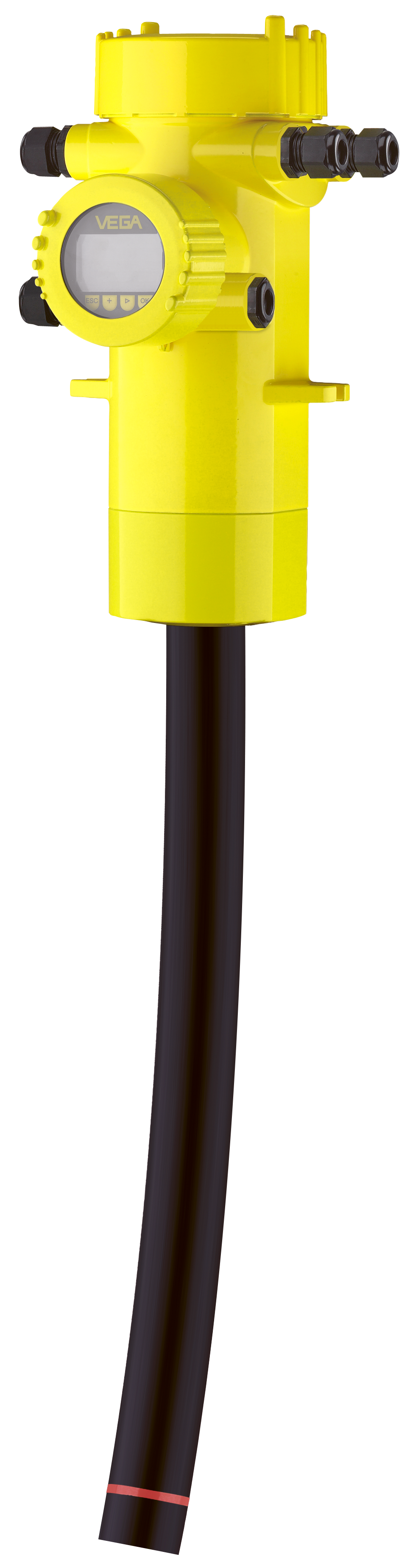
FIBERTRAC 31
Radiation-based sensor for continuous level measurement in coke drums
- Lightweight construction eliminates need for cranes or special rigging for mounting
- Long detector length minimizes the need for additional platform construction
- RS485 gauge to gauge communication network offers extensive diagnostics and reduced troubleshooting time
Measuring range - Distance
7 m
Process temperature
-
Process pressure
-
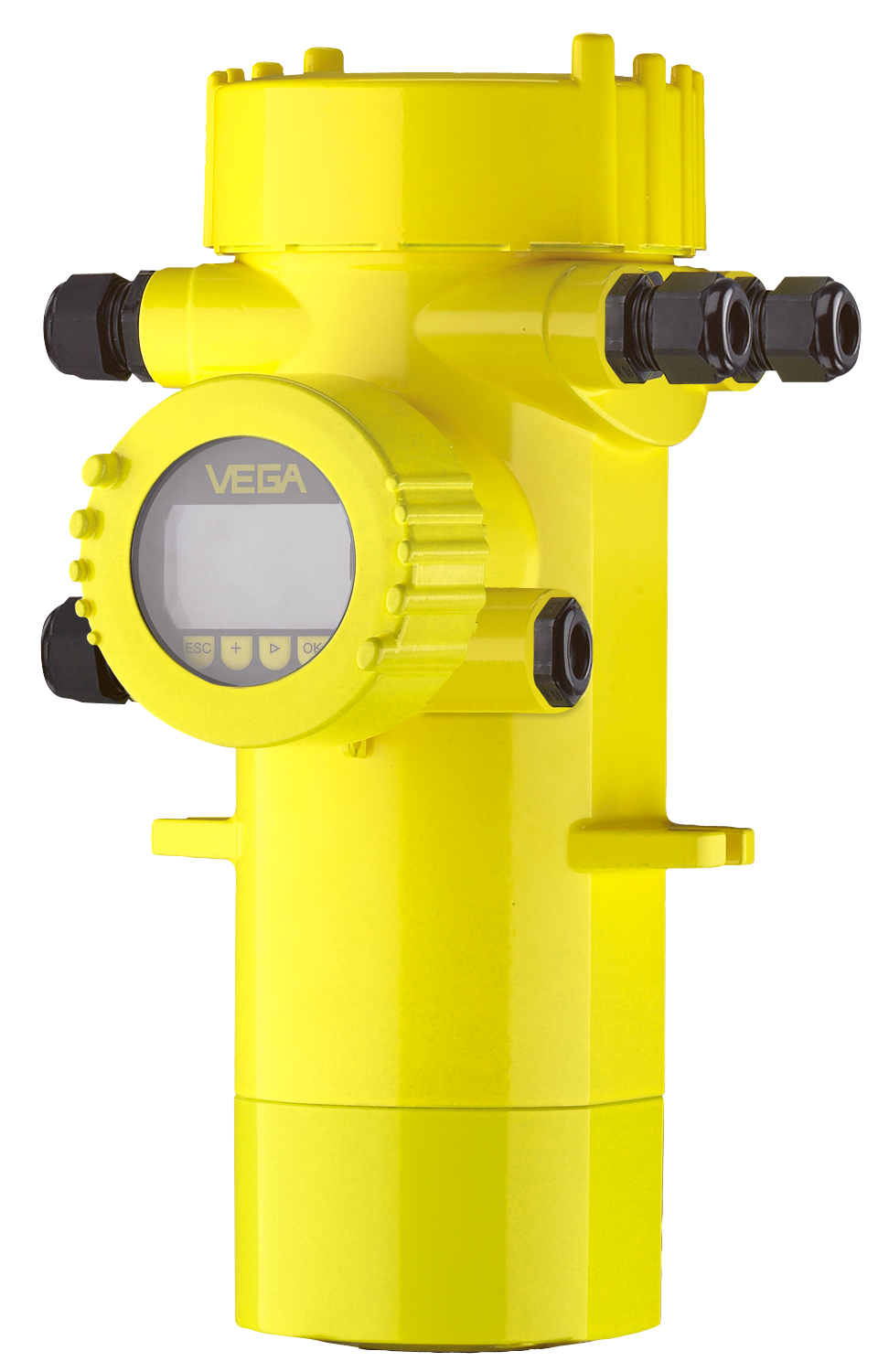
MINITRAC 31
Radiation-based density and point level measurement in coke drums
- Non-contact measurement unaffected by fluid viscosity, deflection or refractive properties
- Monitors anti-foam injection effectiveness
- RS485 gauge to gauge communication network offers extensive diagnostics and reduced troubleshooting time
- Re-zeroing of the system with each cycle improves accuracy
Measuring range - Distance
-
Process temperature
-40 ... 60 °C
Process pressure
-
View more about Density, level measurement and point level detection in coke drums on main site